Manufacturing and transportation are the leading sectors with the highest carbon footprint in the last couple of years. A report by the United States Environmental Protection Agency showed that Industries alone contributed about 24% of the greenhouse gases in the USA in 2020.
However, this can be changed if the various stakeholders in the manufacturing industry leverage the power of technology to reduce the greenhouse gases created by their operations. In this article, we will share how companies in the manufacturing sector can reduce their carbon footprint using technology. Without any further ado, let’s jump right in!
Gradually switching to renewable energy.

Switching to renewable is one of the most effective ways a company can lower its annual carbon footprint. Energy is usually the highest or one of the highest expenses for most companies involved in manufacturing. However, the energy these companies use comes from unclean sources, including burning fossil fuels and coal.
Of course, switching to renewable energy can’t be done overnight since manufacturing requires a lot of energy. Companies can make this switch gradually, starting with components like lighting that don’t need a lot of energy. Installing solar panels on the entire roof of the company premises can produce enough power for lighting and a few other manufacturing tasks.
The short-term costs of switching to renewable energy are usually high, which is why most companies don’t take this step. However, investing in clean energy sources, such as wind turbines and solar, is a worthy investment in the long term. Another indirect benefit of switching to renewable is the improved reputation of the company to potential buyers.
Customers that are cautious about climate change will often prefer dealing with companies that care for the environment. Ultimately this can indirectly impact the company’s sales in the long run.
Switching to EVs in the supply chain

A company’s carbon footprint doesn’t only stop at its direct operations but also includes its supply chain. Suppliers of raw materials and distributors of the final products the company makes should be encouraged to switch to EVs. The good news is that most of the leading companies in the automotive have set up plans to entirely shift to electric vehicles in the next couple of decades.
This shift will help lower the manufacturing costs of EVs hence making it easier and cheaper for companies to opt for them instead of gas cars. The cheapest electric vehicles currently cost over $40,000, almost 50% more than an equivalent gas car. Most individuals and companies still buy gas cars because of the high EV prices. Clearly, the price of EVs is one of the major barriers to entry for most companies.
Having more players in the EV space will also improve the charging network, another factor that could be affecting the adoption of EVs at the moment. Amazon is one of the big companies shifting its supply chain to EVs. Amazon has already ordered over 100,000 EVs to be produced by Rivian by 2040. The company expects thousands of these EVs to be on the road by the end of this year.
Let’s hope other big companies also follow Amazon’s example. When the big players in the game shift to EVs, it becomes more natural for the smaller companies with fewer resources to be motivated to do the same. If you are running a company planning to buy a fleet of new cars, buying EVs would be the best thing you can do to save our environment.
Besides the environmental benefits, EVs are much cheaper to maintain, mainly because they have fewer parts than gas cars. All the parts responsible for keeping the engine moving are eliminated in the case of EVs. In the long run, it is obvious that companies that switch to EVs will incur a relatively lower cost of ownership than those using gas cars.
Using mitigation technologies like Wet scrubbers
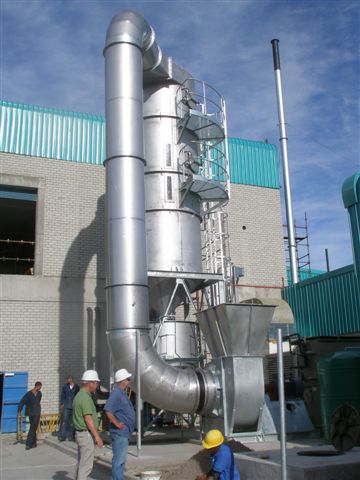
For those who may not know, wet scrubbers are devices designed to remove pollutants from exhaust gases. A significant percentage of greenhouse gases emitted by companies in manufacturing are usually through air pollution. Wet scrubbers can be put at the exhaust pipes of the different equipment to remove dangerous gases before the air goes into the atmosphere.
Using wet scrubbers is a popular solution because they remove pollutants from exhaust gas in one step and not two, which lowers the implementation costs. It is also important to note that paying fines for violating clean air rules is much more costly when compared to installing wet scrubbers in the manufacturing system.
Besides wet scrubbers, other mitigation technologies that companies can use include;
- Catalytic Oxidizers: This equipment uses a metal catalyst and high heat to oxidize volatile organic compounds (VOCs) and hazardous air pollutants (HAPs) into water and carbon dioxide.
- Regenerative thermal oxidizers (RTOs): These use extreme heat to remove contaminants from factory byproducts, including exhaust gases. RTOs need significantly more heat than Catalytic Oxidizers.
- Rotary concentrator systems: These systems work by pushing air through a rotating drum, forcing contaminants out of the air and into a hydrophobic media, where an oxidizer destroys them.
Using data analytics to optimize production
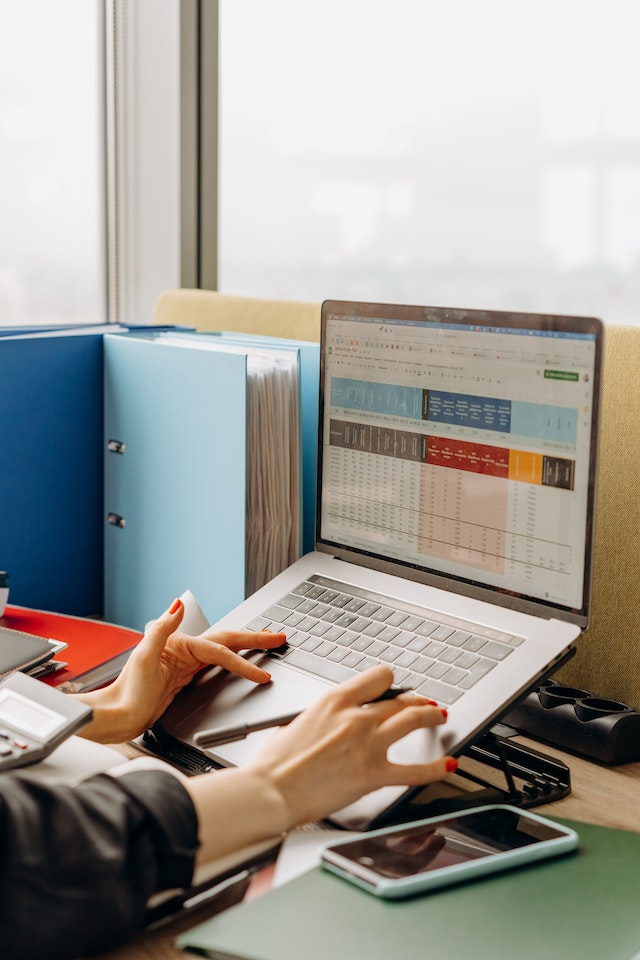
It is important for a company to manufacture products that do not exceed its public demand. Producing more than your market needs often leads to unnecessary energy and raw materials waste that could have been avoided with better planning. The good news is that companies now have access to sophisticated tools that they can use to predict future trends.
Predictive analytics tools use artificial intelligence and machine learning technologies to give insights into the demand for a particular product in the next couple of months. This allows the responsible parties in the company to optimize the production process based on this data. The accuracy of these predictive analytics systems usually depends on how much data you feed them. That’s why they get better at providing accurate insights over time.
Using automation
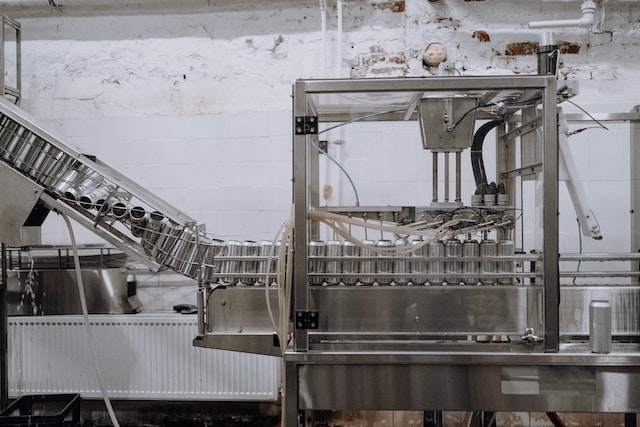
One of the benefits of implementing automation in factories is the fact that they have the potential to lower carbon emissions significantly. With automation, most of the operations are done more precisely and efficiently, reducing the energy required to operate the manufacturing plant. Lower energy consumption significantly lowers the carbon footprint of the company. Automation also enables precise scheduling of maintenance tasks, so machines are only maintained at the most appropriate and not after a fixed period.
It should be noted that maintenance of equipment requires using energy and oil products that are usually not good for the environment. Eliminating the need for frequent maintenance will significantly lower energy and consumables used in maintenance. Automated equipment is also more efficient and uses significantly lower energy than manual equipment.
Use smart IoT devices to monitor energy usage.
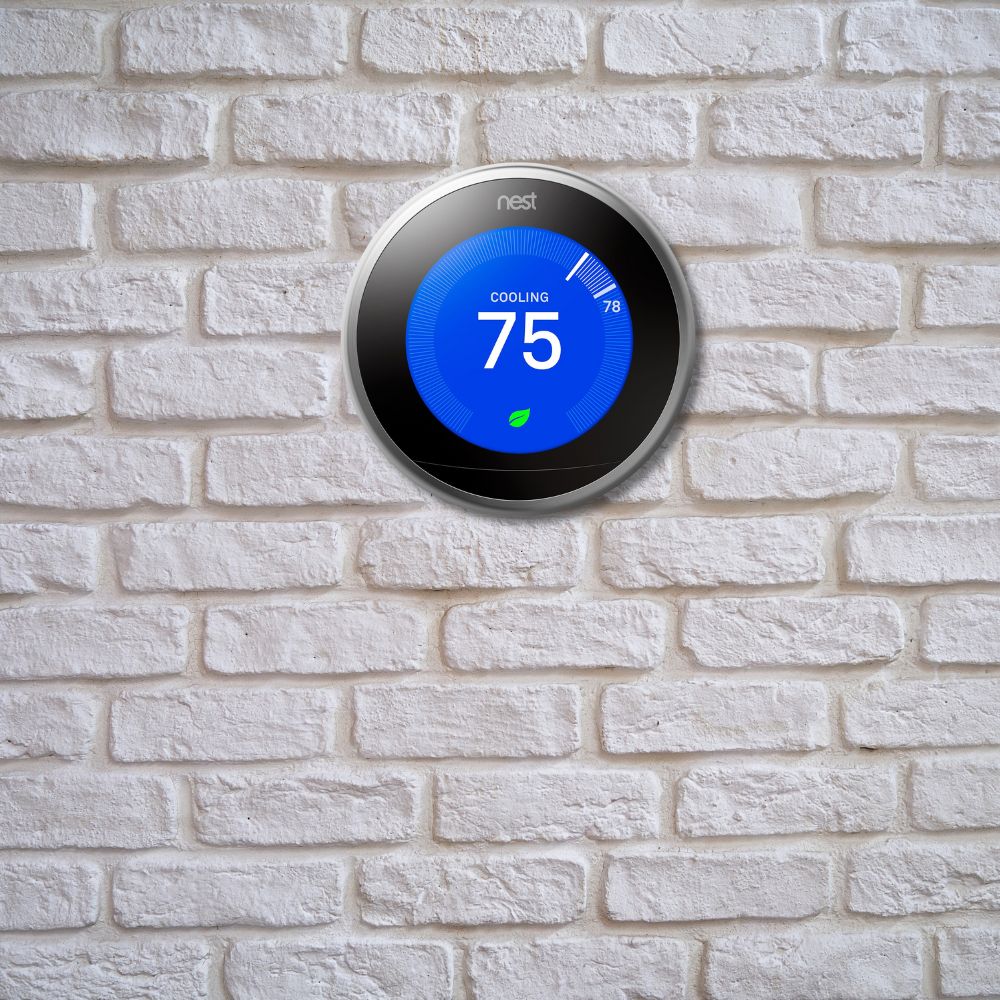
One of the easiest ways to save energy in any manufacturing plant is by turning off equipment and devices that are not needed. IoT smart devices can be used to ensure that air conditioning and other devices are turned on only when needed. Ultimately, this can save the company’s monthly and annual energy bills.
You can also use smart meters to constantly give you the real-time power consumption of the different devices in the manufacturing plant. This allows you to identify the equipment that takes up the most power and then devise solutions for lowering this consumption. This may include long-term solutions such as replacing the equipment with more efficient options.
There are also smart devices that can be paired with large batteries to store energy during off-peak hours so that the load on the grid is reduced during peak hours. When demand for energy is high, almost every power generating plant is put into use, often including the dirty ones. So, using energy during off-peak can reduce your company’s carbon printer since this energy is cleaner.
On top of lowering your carbon footprint, using energy during off-peak hours also reduces your annual energy bill. At the end of the day, deploying a smart system that can switch back and forth between batteries and grid energy depending on the overall energy demand will save your company money and also lower your carbon footprint.
Use 3D printing
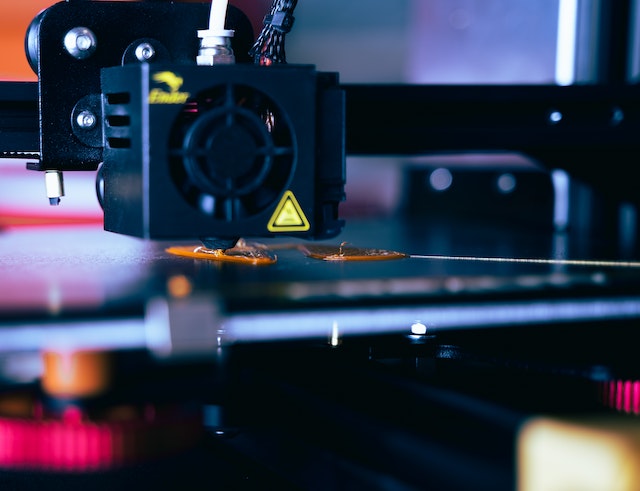
3D printing is one of the newer manufacturing processes that savvy companies already use. One of the main benefits of using 3D printing is that it lowers the number of processes involved in the production process of a given item. Fewer processes result in lower energy consumption, reducing the company’s overall carbon footprint.
3D printing is also known for minimizing materials wasted during the manufacturing process. Manufacturing processes that involve cutting off material to create the desired shape of the product often lead to a lot of waste, which is not good for the environment. Creating parts with 3D printers wastes almost no materials, reducing the number of raw materials required to create products compared to other manufacturing processes.
A number of big companies in different industries are already using 3D printing to create several parts of their products. Boeing was one of the early adopters of 3D printing technology and has made more than 20,000 3D-printed parts for ten different military and commercial planes. Nike also uses 3D printing to create specific components of its shoes.
Overall, many companies are already enjoying the benefits of 3D printing, including lowering their carbon footprint. Of course, certain parts can’t be made by 3D printing. As a company, you need to figure out the best use cases of 3D printing so that you use it to lower material requirements and energy consumption for those specific scenarios.
Use cloud computing where possible.

Modern manufacturing plants rely on huge amounts of data to optimize operations. Getting sense out of this data requires huge amounts of computational power, leading to more energy consumption. However, companies can save money and lower their carbon footprint if they use cloud computing over on-premise computing. Here is why.
Most popular cloud computing platforms, including AWS, Microsoft Azure, and Google Cloud, have invested heavily in renewable energy. Almost all the data centers of these companies are powered by clean energy. Using their servers for your computational needs will significantly lower your carbon footprint since most of the energy you will be using is from clean sources.
These platforms also provide their users with detailed information regarding the emissions generated by their computation tasks. This information can be used to make more conscious decisions to minimize energy consumption. Some of these choices may include using more energy-efficient models and programming languages.
Final thoughts
Companies that adopt any or possibly all the above strategies can significantly lower their carbon footprint. The suggested solutions can reduce a company’s carbon footprint by lowering energy consumption, which is often the major contributor to carbon emissions generated from manufacturing plants.
Some of the suggested solutions also reduce the waste of materials during manufacturing. This reduces the number of raw materials needed to achieve the same results, lowering a company’s carbon footprint.